When it comes to manufacturing parts and components, selecting the right stamping process is crucial. Two of the most commonly used stamping techniques are cold stamping and hot stamping. Both methods have their own unique advantages, and the choice between the two depends on several factors such as material type, design complexity, production volume, and cost.
This article will guide you through the differences between cold stamping and hot stamping to help you determine which method is best suited for your project. Whether you are looking for metal stamping service for automotive parts, consumer electronics, or any other industry, understanding these processes is key to making an informed decision.
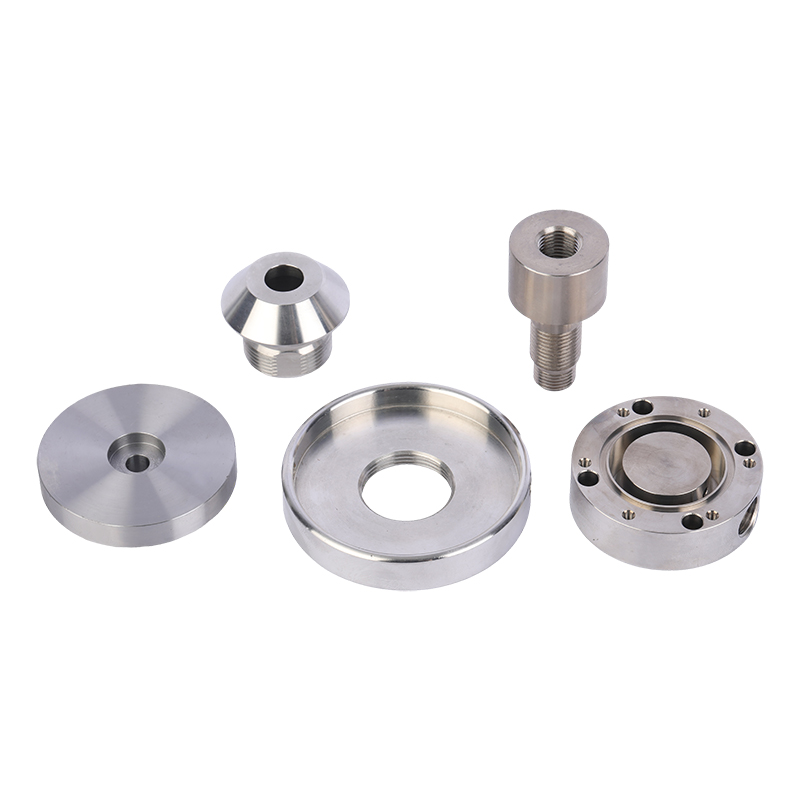
What is Cold Stamping?
Cold stamping, also known as cold forming, is a process in which sheet metal is deformed at room temperature to create a variety of metal stamping parts. It is a versatile process used for producing high-precision parts with tight tolerances. This technique is typically applied to materials such as steel, aluminum, and copper alloys.
Advantages of Cold Stamping:
- Cost-Effective: Since it doesn’t require heating the material, cold stamping tends to be more economical, especially for high-volume production.
- High Precision: Cold stamping is ideal for producing metal precision stamping parts with tight tolerances and clean surface finishes.
- Better Surface Quality: The process preserves the material’s surface integrity, which is important for parts that need a smooth finish.
Cold stamping is commonly used in the production of all metal stamping parts for industries such as automotive, electronics, and appliance manufacturing. Components such as brackets, connectors, and enclosures are frequently produced using cold stamping.
What is Hot Stamping?
Hot stamping, in contrast, involves heating the material to high temperatures before it is deformed in the stamping die. This process allows the metal to become more malleable and easier to shape, making it suitable for complex or thicker parts. Hot stamping is often used with high-strength steels and other tough alloys that would be too difficult to shape at room temperature.
Advantages of Hot Stamping:
- Ability to Form High-Strength Materials: Hot stamping is particularly useful when working with materials that have higher strength, such as high-strength steel or aluminum. The process improves the material’s ductility, enabling the creation of more intricate designs.
- Stronger Parts: Hot stamping often results in parts with enhanced material strength. This makes it ideal for critical automotive components, structural parts, and other high-stress applications.
- Complex Shapes: The high temperature allows for easier forming of complex geometries and thicker materials, which would otherwise be challenging to produce using cold stamping.
Hot stamping is used in industries such as automotive manufacturing, where parts like bumpers, structural frames, and brackets require both strength and precision. Parts produced through hot stamping often need to undergo further heat treatment to achieve optimal material properties.
Key Differences Between Cold Stamping and Hot Stamping
The primary differences between cold stamping and hot stamping lie in their working temperatures, material properties, and suitable applications. Here’s a breakdown:
1. Temperature:
- Cold Stamping: Performed at room temperature, typically between 15°C and 30°C.
- Hot Stamping: Involves heating the metal to temperatures between 800°C and 1000°C, depending on the material.
2. Material Properties:
- Cold Stamping: Works best with materials that can be easily deformed at room temperature. The resulting parts maintain the original material properties.
- Hot Stamping: Ideal for materials that are difficult to form at room temperature, such as high-strength steels. The heating process alters the material’s properties, improving its strength and ductility.
3. Precision:
- Cold Stamping: Delivers superior precision, making it ideal for parts that require tight tolerances and minimal post-processing.
- Hot Stamping: While it can form complex shapes, it may sacrifice some precision due to the material’s increased malleability at high temperatures.
4. Production Speed:
- Cold Stamping: Faster compared to hot stamping, as it doesn’t require time for heating or cooling.
- Hot Stamping: Generally slower because of the heating and cooling processes, making it more suitable for lower-volume production runs.
5. Cost:
- Cold Stamping: Generally more cost-effective for high-volume production due to its faster turnaround time and lack of need for heating equipment.
- Hot Stamping: More expensive due to the higher energy costs for heating the material and the specialized equipment required.
Factors to Consider When Choosing Between Cold and Hot Stamping
When selecting the right stamping process for your project, there are several factors to keep in mind. Your choice will depend on your specific needs, the material you’re working with, and the type of part you need to create.
1. Material Type and Strength
The choice between cold and hot stamping often depends on the material you’re using. For softer metals or thinner materials, cold stamping is usually the preferred option. However, for high-strength materials or thicker components, hot stamping may be necessary to ensure the material can be formed without cracking or breaking.
2. Design Complexity
If your part requires intricate shapes or thick material, hot stamping can offer more flexibility. It allows you to form complex shapes that would be difficult to achieve with cold stamping. On the other hand, simple, high-precision parts with minimal material thickness are often better suited for cold stamping.
3. Precision Requirements
If your project demands high precision and tight tolerances, metal precision stamping with cold stamping will be the better choice. Cold stamping offers better control over dimensions, which is critical for applications where exact measurements are essential.
4. Production Volume
For high-volume production, cold stamping is typically more efficient and cost-effective due to its faster cycle times and lower energy requirements. For lower-volume production or when manufacturing parts that require stronger materials, hot stamping may be more appropriate.
Which Stamping Process is Best for Your Project?
When deciding between cold stamping and hot stamping, it’s important to consider the specific needs of your project. Both methods offer unique advantages, and choosing the right one depends on a variety of factors. Let’s summarize the decision-making process based on the following aspects:
1. Cost Efficiency
For large-scale production, cold stamping tends to be more cost-efficient due to its quicker turnaround and lower energy requirements. It’s the best option when cost-effectiveness is a priority, especially for parts that don’t require the enhanced strength or complex shapes that hot stamping can provide.
However, if your project involves high-strength materials, and you require durable, high-performance parts, hot stamping might be worth the extra investment. While it may come with higher energy costs and longer processing times, the strength and precision it provides for complex shapes make it a valuable option.
2. Material Requirements
Your material choice will significantly influence the stamping process. If you’re working with materials like aluminum, steel, or copper alloys, cold stamping will likely be your go-to method. However, if you need to work with tougher, high-strength materials like high-strength steel, hot stamping may be required.
It’s essential to consult with a metal stamping service provider who has experience with your material, as they can offer insights into the most effective method for achieving the desired results.
3. Part Complexity
For parts that require intricate shapes and high-strength properties, hot stamping is the ideal choice. It’s particularly beneficial for automotive and aerospace applications where parts must be both strong and complex. For less intricate designs or parts that require high precision and tight tolerances, cold stamping would be more appropriate.
4. Production Time and Volume
If you have a high volume of parts to produce and need to keep production times short, cold stamping is likely the best method. It’s quicker and doesn’t involve the lengthy heating and cooling processes required in hot stamping. However, if the part design is complex or involves heavy-duty materials, hot stamping can still be the better choice despite the longer cycle time.
5. Precision
For parts that need to adhere to strict tolerances, cold stamping excels. The process is capable of achieving high precision, making it ideal for small, detailed components used in electronics, medical devices, and other industries requiring minimal deviation in part dimensions.
In comparison, hot stamping may not achieve the same level of precision, but it offers benefits in material strength and shape complexity that cold stamping cannot match.
Conclusion: Making the Right Choice
The decision between cold stamping and hot stamping ultimately comes down to the specific requirements of your project. If you need metal stamping parts that are cost-effective, high-precision, and suitable for mass production, cold stamping is often the best option. However, if your project demands parts with enhanced strength, durability, and complex geometries, hot stamping will provide the necessary performance and reliability.
For businesses seeking a metal stamping service, it’s essential to work with a trusted metal stamping manufacturer or metal stamping supplier who can assess your project’s needs and recommend the best solution. Whether you need all metal stamping for an automotive component or metal precision stamping for a delicate part, a professional stamping service can guide you toward the right choice.