Choosing the right materials for the stamping process is critical for ensuring high-quality results and optimal performance. For industries ranging from automotive to electronics, understanding the characteristics of various materials helps in selecting the most suitable options. This guide will discuss the best materials for stamping, the factors to consider, and why partnering with an experienced metal stamping company is essential for success.
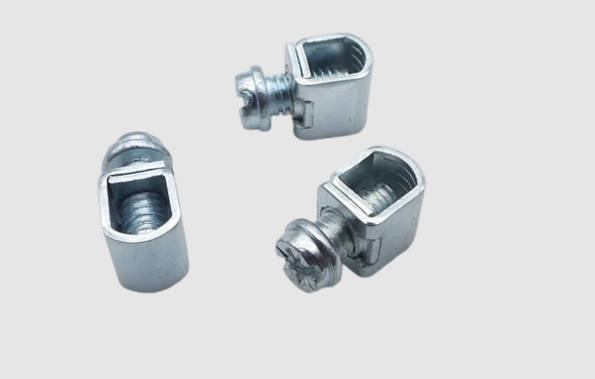
Key Characteristics to Look for in Stamping Materials
When selecting materials for the stamping process, it’s important to focus on specific properties that ensure efficiency and precision. The main characteristics to consider include:
- Ductility: The ability of a material to be stretched or formed without breaking is vital for intricate stamping parts.
- Strength: Materials must have the right balance of tensile and yield strength to maintain shape during and after stamping.
- Durability: Ensuring that the final product can withstand its intended application without degrading.
These characteristics influence the choice of materials and determine how well they can be shaped using a metal stamping service.
Commonly Used Metals for Stamping
Steel (Carbon and Stainless Steel)
Steel is one of the most popular materials for stamping metal due to its strength, versatility, and wide availability.
- Advantages:
- High Strength: Steel is known for its excellent mechanical properties, making it suitable for heavy-duty applications.
- Diverse Grades: Both carbon steel and stainless steel are available in numerous grades, allowing for customized solutions based on specific stamping parts needs.
- Applications: Common in the production of automotive components, industrial machinery, and structural frameworks.
Steel is widely used by a metal stamping company to produce durable and long-lasting parts for various sectors.
Aluminum
Aluminum is another commonly chosen metal for stamping due to its lightweight and corrosion-resistant properties.
- Advantages:
- Lightweight: Significantly reduces the weight of the final product without compromising strength.
- Corrosion Resistance: Ideal for applications that require exposure to environmental elements.
- Applications: Frequently used in the aerospace industry, consumer electronics, and transportation.
Aluminum’s versatility ensures it is frequently featured in the repertoire of a reputable stamping metal service.
Copper and Its Alloys (Brass and Bronze)
Copper and its alloys, such as brass and bronze, are often chosen for their electrical conductivity and aesthetic appeal.
- Advantages:
- High Conductivity: Copper is unparalleled in its electrical and thermal conductivity, making it ideal for electrical stamping parts.
- Aesthetic Quality: Brass and bronze offer a unique appearance suitable for decorative purposes.
- Applications: Widely used in electrical components, plumbing fixtures, and decorative hardware.
Nickel Alloys
Nickel Alloys are known for their exceptional heat resistance and strength.
- Advantages:
- Heat Resistance: Can withstand high temperatures without losing structural integrity.
- Durability: Perfect for demanding environments where performance and longevity are essential.
- Applications: Commonly used in turbine engines, industrial equipment, and high-performance parts.
A reliable metal stamping service often includes nickel alloys in their materials portfolio for specialized applications.
Non-Metal Materials for Specialized Stamping
While metals are predominant in the stamping industry, non-metal materials such as plastics and composites are also used for specific applications.
Plastics (Thermoplastics)
Thermoplastics are increasingly being used in the stamping process for lightweight, cost-effective solutions.
- Advantages:
- Low Cost: More affordable compared to metals, making them ideal for mass production.
- Lightweight: Suitable for products where weight reduction is a priority.
- Applications: Used in consumer products, medical device housings, and packaging.
Composites
Composites are engineered materials that combine different substances to achieve superior properties.
- Advantages:
- Customizability: Can be tailored for specific mechanical properties.
- Durability: Often more resistant to wear and tear compared to some metals.
- Applications: Ideal for high-precision parts in aerospace and specialized industries.
Factors to Consider When Choosing Materials
Production Volume
The volume of production plays a crucial role in selecting the right material. For high-volume production, cost-effectiveness and ease of stamping metal are key considerations.
Cost Efficiency
Balancing performance with cost is essential. While certain metals may provide enhanced features, they may not be budget-friendly for large-scale stamping parts. Partnering with an experienced metal stamping company helps in evaluating options for the best value.
End-Use Requirements
The intended application of the stamped parts should guide material selection. Products exposed to moisture or chemicals, for instance, require materials with specific corrosion resistance.
Compatibility with Stamping Equipment
Material hardness and thickness must align with the capabilities of the stamping equipment to avoid excessive wear and maintain production quality.
Conclusion
Choosing the right material for the stamping process is crucial for ensuring the production of high-quality, durable, and cost-effective components. Understanding the properties of steel, aluminum, copper, and non-metal alternatives allows for informed decision-making. Collaborating with a reputable metal stamping company ensures that you access expert advice, high-quality stamping metal services, and materials best suited for your specific application. This comprehensive approach ensures the production of superior stamping parts that meet and exceed industry standards.