Introduction
CNC machining has revolutionized manufacturing, enabling the creation of highly precise and complex parts used in a wide range of industries. From aerospace and automotive to medical and electronics, CNC machining services are in high demand for producing custom components with tight tolerances and intricate geometries. However, understanding what drives the cost of CNC machined parts is essential for buyers seeking affordable yet high-quality solutions.
This article will explore the primary factors that influence CNC machined part costs, helping potential buyers make informed decisions and optimize their designs for cost-effectiveness. Key cost drivers such as material selection, part complexity, production volume, and post-processing will be discussed to guide those in need of CNC machining services, including cnc precision machining and cnc metal machining.
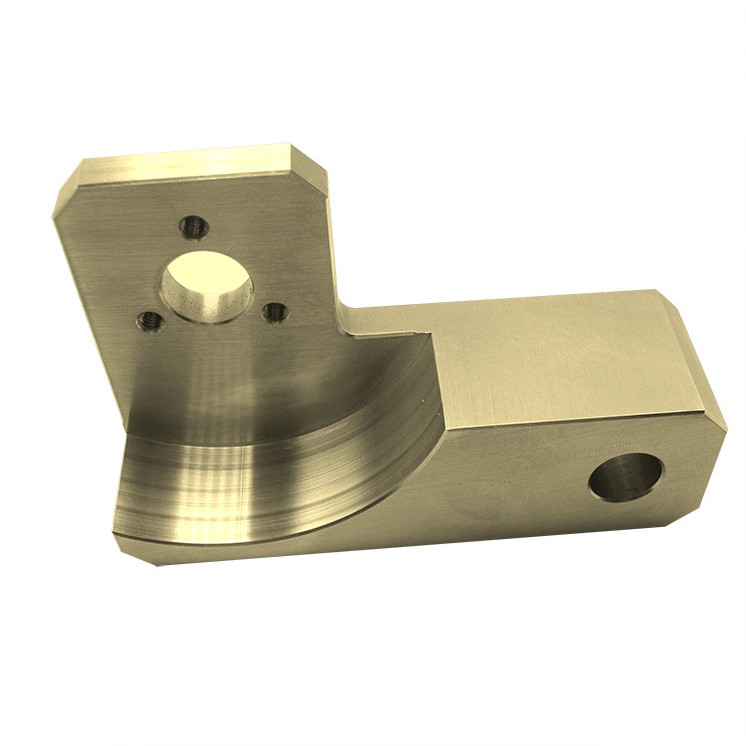
1. Material Selection
One of the most significant factors impacting the cost of CNC machined parts is the choice of material. CNC machining can accommodate a variety of materials, including metals, plastics, and composites, each with distinct cost implications. For example, common metals like aluminum are relatively inexpensive and easy to machine, making them a cost-effective option. However, materials like titanium or stainless steel can be significantly more expensive due to their hardness and the difficulty of machining them.
- Aluminum: Lightweight, corrosion-resistant, and easy to machine, aluminum is one of the most popular materials for CNC metal machining.
- Steel: Stronger than aluminum but more challenging to machine, resulting in longer machining times and higher costs.
- Titanium: Extremely strong and corrosion-resistant, but its high hardness makes it difficult and costly to machine.
- Plastics: Plastics like ABS or nylon are often cheaper to machine, but they may not be suitable for high-stress applications.
In addition to the base cost of materials, the machinability of the chosen material affects the overall CNC machining service cost. Harder materials tend to wear out cutting tools faster and require more time for cnc precision machining, increasing both tooling and labor expenses.
2. Part Design and Complexity
The complexity of a part’s design plays a crucial role in determining the cost of CNC machining. Parts with intricate geometries, fine details, or internal cavities require more advanced machining techniques, such as 5 axis cnc machining, which can significantly increase production time and cost.
- Complex Geometries: Parts with multiple surfaces, deep cuts, or undercuts may require multi-axis machining, leading to longer setup times and additional machining operations.
- Tight Tolerances: Achieving extremely tight tolerances requires more precise machining and may involve slower feed rates or multiple passes, increasing machining time.
- Design for Manufacturability (DFM): Simplifying part designs without compromising functionality can help reduce costs. Collaborating with CNC machining service providers during the design phase can ensure the part is optimized for manufacturability.
In CNC machining, every feature of a part, from holes and threads to surface finishes, adds complexity. The more complex the part, the more time and resources are required, impacting the final cost of cnc metal machining services.
3. Tolerance and Surface Finish Requirements
The level of precision required for a CNC machined part, as well as the desired surface finish, can have a significant effect on costs. Tighter tolerances and smoother finishes require more detailed work and can increase machining time, tooling wear, and inspection processes.
- Tolerances: Tight tolerances (+/- 0.001 inches or less) necessitate additional quality control checks and more precise machining techniques. The cost increases as the tolerance range narrows, particularly for critical components in industries like aerospace or medical devices.
- Surface Finish: A smooth or polished surface finish often requires additional finishing operations such as polishing or grinding, adding to the overall cost. The type of surface finish required—whether matte, smooth, or highly polished—also determines the type of post-processing needed, further influencing the price.
Balancing the need for high precision with the realities of cost is essential for buyers. Unless the application demands extreme precision, opting for standard tolerances and surface finishes can help reduce cnc precision machining expenses.
4. Quantity of Parts (Batch Size)
The number of parts required in a single order, often referred to as batch size, plays a critical role in the overall cost of CNC machining. Larger production volumes allow for cost-saving measures such as reducing setup time and spreading tooling costs over a greater number of parts.
- Low-Volume Production: For custom or prototype parts, low-volume production can be expensive. Each part requires a full setup of the CNC machine, and because the setup cost is not spread across a large quantity, the per-unit cost remains high.
- High-Volume Production: In contrast, larger production runs benefit from economies of scale. Once the machine is set up, it can produce parts continuously, lowering the overall cost per unit. CNC machining service providers often offer discounted rates for larger orders to reflect these efficiencies.
For buyers, it’s crucial to assess their part needs and decide whether to invest in larger batches to lower the per-unit cost or stick with smaller, more expensive batches for custom orders.
5. Machining Time and Complexity of Operations
Machining time is one of the most direct cost drivers in CNC machining services. The longer it takes to machine a part, the higher the cost will be. Several factors influence machining time, including the complexity of operations required, the type of machine used, and the number of setups needed.
- Multi-Axis Machining: For intricate parts requiring 5 axis cnc machining, the complexity of the operations involved significantly increases machining time. While 5 axis cnc machining allows for greater flexibility in producing complex shapes, it also requires more programming and tool changes, which adds to the cost.
- Tool Changes: Each tool change required during machining interrupts the process, adding both time and labor. Parts with multiple features may need different tools for each feature, further increasing machining time.
- Programming and Setup Time: For complex parts, significant time may be spent programming the CNC machine and setting up fixtures or jigs. These initial steps can contribute to the overall cost, especially in small-batch production.
To reduce machining time and costs, buyers can work with their CNC machining service provider to simplify part design or eliminate unnecessary features, ensuring the part is manufactured as efficiently as possible.
6. Post-Processing and Finishing Services
After CNC machining, many parts require additional post-processing to meet functional or aesthetic requirements. These services can include heat treatment, anodizing, plating, or painting, all of which come with their own costs.
- Heat Treatment: Some metal parts may need to be heat-treated to improve hardness or durability. This process adds both time and expense to the production cycle.
- Anodizing and Plating: For parts that require corrosion resistance or a specific finish, anodizing or plating is often necessary. These processes, especially for decorative finishes, can significantly increase costs.
- Painting or Powder Coating: Aesthetic finishes like painting or powder coating add to the overall price. The complexity and number of coatings required will also influence the final cost.
Buyers should consider their post-processing needs carefully. While these services are often essential for part performance or appearance, eliminating unnecessary post-processing steps can reduce costs without compromising on quality.
7. Tooling and Setup Costs
Tooling and setup costs are an important consideration in CNC machining, especially for custom parts. Custom fixtures, jigs, or specialized cutting tools may be required to machine certain parts, leading to higher initial costs.
- Custom Tooling: If a part requires unique tooling, the buyer may incur additional costs for the creation of these tools. This is particularly common in highly specialized cnc metal machining or in applications where specific material properties must be met.
- Setup Time: CNC machines require precise setup before machining begins, especially for complex parts. The cost of setup is usually fixed, meaning it can have a higher impact on smaller batch sizes where the cost is not spread out over many parts.
Working closely with a CNC machining service provider to minimize tooling requirements and setup complexity can help reduce costs, particularly for low-volume orders.
8. Lead Time and Urgency
The time frame in which the parts are needed can significantly affect the cost. CNC machining services often charge a premium for rush orders that require expedited production.
- Standard Lead Times: If the project timeline allows for standard production times, the cost will typically remain lower. Buyers should plan ahead to ensure that they can take advantage of more cost-effective production schedules.
- Rush Orders: When parts are needed urgently, the service provider may need to rearrange their production schedule or work overtime, both of which can increase costs. Rush orders can result in higher labor and operational costs due to the need for quicker turnaround times.
Whenever possible, buyers should plan their projects in advance to avoid premium charges for expedited services.
Conclusion
Understanding the factors that influence the cost of CNC machined parts is essential for buyers looking to optimize their purchasing decisions. From material selection and part design to batch size and post-processing, each decision has a direct impact on the final cost of CNC machining services.
By working closely with a trusted CNC machining service provider, buyers can make informed choices about material options, design optimizations, and production volumes to balance quality and cost. Whether you’re seeking 5 axis cnc machining for complex parts or cnc precision machining for high-tolerance components, understanding these cost drivers can help you achieve both high performance and cost-effectiveness in your CNC machined parts.
In summary, when looking for cost-effective cnc metal machining, it’s important to consider material properties, part complexity, production volume, and any post-processing requirements, while maintaining a strong relationship with the CNC machining service provider to ensure the best results.