Introduction
Metal stamping is a vital manufacturing process that transforms flat metal sheets into precise, functional components using specialized dies and presses. This technique is widely used across industries such as automotive, electronics, aerospace, medical, and appliances, where precision and durability are non-negotiable. For those exploring metal stamping services, understanding the distinction between Progressive Die Stamping and Traditional Metal Stamping is key to selecting the most suitable method for your project. This guide dives deep into both processes, comparing their features, costs, and applications to help you make an informed choice when partnering with a metal stamping company.
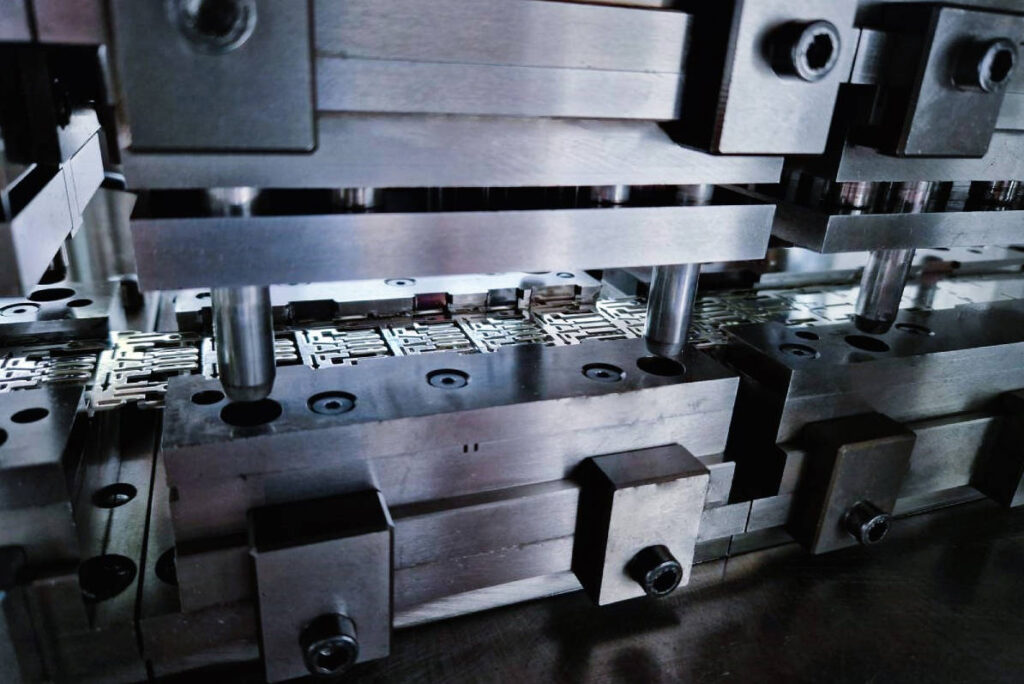
What is Metal Stamping?
At its core, metal stamping involves shaping metal sheets into desired forms through a series of operations like cutting, bending, punching, or forming. The metal stamping process relies on dies—custom tools that define the shape—and presses that apply force to mold the metal. Whether you need brackets, connectors, or enclosures, choosing the right metal stamping solutions ensures high-quality results while balancing cost and efficiency.
Overview of Traditional Metal Stamping
Traditional Metal Stamping encompasses methods like single-stage or transfer die stamping, where each shaping operation occurs independently. This approach often involves multiple dies and manual intervention between stages.
- Process: Metal sheets are processed through individual dies for each step—e.g., cutting followed by bending.
- Key Characteristics:
- Ideal for low to medium production volumes.
- Offers flexibility for simple or custom parts.
- May incur higher labor costs due to multiple setups.
- Common Use Cases: Prototyping, small-batch production, or parts with straightforward designs.
This method shines when customization and adaptability outweigh the need for speed or high output, making it a popular choice for bespoke projects with a metal stamping manufacturer.
Overview of Progressive Die Stamping
Progressive Die Stamping, on the other hand, is a streamlined, automated process that uses a single die with multiple stations. As a metal strip advances through the die, each station performs a specific task in sequence.
- Process: The metal strip progresses through the die, with stations cutting, bending, or forming it step-by-step.
- Key Characteristics:
- High-speed and automated, perfect for large-scale production.
- Lower labor costs thanks to automation.
- Higher initial investment in complex tooling.
- Common Use Cases: Mass production of intricate parts like automotive components, connectors, or appliance hardware.
For projects demanding consistency and efficiency, Progressive Die Stamping is a top-tier option offered by leading metal stamping services.
Key Differences Between Progressive Die Stamping and Traditional Metal Stamping
To pick the best metal stamping process for your needs, it’s essential to grasp how these methods differ. Here’s a detailed comparison:
Aspect | Progressive Die Stamping | Traditional Metal Stamping |
Production Volume | Excels in high-volume runs (thousands to millions) | Suited for low to medium volumes or prototyping |
Tooling Costs | Higher upfront costs for custom dies | Lower initial costs but higher per-part expenses |
Speed and Efficiency | Faster with a continuous, automated workflow | Slower due to multiple setups or manual steps |
Part Complexity | Perfect for complex parts with multiple operations | Better for simpler or custom designs |
Labor Requirements | Minimal due to automation | Often requires more manual effort |
Material Utilization | Optimized with less waste | May produce more scrap depending on the setup |
Google Featured Snippet Potential: Progressive Die Stamping is best for high-volume production of complex parts, offering speed and cost savings, while Traditional Metal Stamping suits low to medium volumes and custom projects with its flexibility and lower upfront costs.
Advantages and Disadvantages
Progressive Die Stamping
- Advantages:
- Superior efficiency and cost-effectiveness for large runs.
- Uniform quality across all parts.
- Reduced labor costs through automation.
- Disadvantages:
- Significant initial tooling expenses.
- Limited flexibility for design adjustments.
- Less practical for small batches.
Traditional Metal Stamping
- Advantages:
- Affordable initial tooling costs.
- Highly adaptable for small runs or custom parts.
- Great for prototyping and rapid design changes.
- Disadvantages:
- Slower production pace.
- Higher labor costs.
- Less efficient for high-volume needs.
These trade-offs highlight why aligning your project goals with the right metal stamping solutions is critical.
Choosing the Right Method for Your Project
Deciding between Progressive Die Stamping and Traditional Metal Stamping hinges on several factors:
- Production Volume: Opt for Progressive for high volumes and Traditional for smaller runs.
- Part Complexity: Progressive handles complex, multi-step parts; Traditional suits simpler or unique designs.
- Budget: Progressive involves higher initial costs but saves money per part in large runs; Traditional is cheaper upfront but costlier per unit.
- Lead Time: Progressive speeds up production after tooling; Traditional offers faster setup for small batches.
- Material: Both methods work with metals like copper, aluminum, and stainless steel, though Progressive may excel with thinner sheets.
For instance:
- Choose Progressive Die Stamping for mass-producing automotive brackets or electronic connectors.
- Select Traditional Metal Stamping for custom medical prototypes or low-volume aerospace parts.
Engaging a metal stamping manufacturer like Kaiyan Hardware can refine this decision, tailoring metal stamping services to your specific needs.
Common User Questions Answered
Which method is more cost-effective?
Progressive Die Stamping wins for high-volume production with lower per-part costs, while Traditional Metal Stamping is more economical for low-volume or custom jobs due to reduced initial investment.
How long does tooling take?
Tooling for Progressive Die Stamping may take weeks to months given the die’s complexity, whereas Traditional Metal Stamping tooling is faster for simpler setups.
Can I switch methods mid-project?
Switching mid-project is expensive due to new tooling requirements. Early planning with your metal stamping company is crucial to avoid such costs.
What materials are compatible?
Both methods support metals like copper, aluminum, and stainless steel. Progressive Die Stamping often handles thinner materials with greater precision.
How do I ensure quality?
Partner with a metal stamping manufacturer offering ISO 9001 certification and advanced tools—like Kaiyan Hardware’s 2.5D projectors and hardness testers—for consistent quality.
Why Work with a Professional Metal Stamping Service?
Collaborating with a reputable metal stamping company like Kaiyan Hardware brings multiple advantages:
- Expertise in both Progressive Die Stamping and Traditional Metal Stamping.
- ODM/OEM offerings for customized metal stamping solutions.
- Robust quality control with ISO 9001 standards and cutting-edge testing equipment.
- Industry experience spanning automotive, medical, electronics, and beyond.
Effective communication with your provider ensures your project aligns with budget, timeline, and quality goals.
Conclusion
To wrap up, Progressive Die Stamping is the champion of high-volume, complex part production, delivering speed and cost efficiency, while Traditional Metal Stamping offers flexibility for smaller runs or custom designs. Assess your project’s volume, budget, and timeline to determine the best fit. Consulting a trusted metal stamping manufacturer like Kaiyan Hardware can provide expert guidance and top-notch results.
Ready to start? Contact Kaiyan Hardware for personalized metal stamping services today.