Metal stamping is a crucial manufacturing process used to shape and form metal into specific parts and components. As industries increasingly rely on metal stamping for their production needs, ensuring the quality of stamped products becomes paramount. Quality control (QC) plays a vital role in maintaining product reliability, minimizing waste, and meeting customer specifications. This article aims to guide potential buyers on how to effectively implement quality control measures in metal stamping processes.
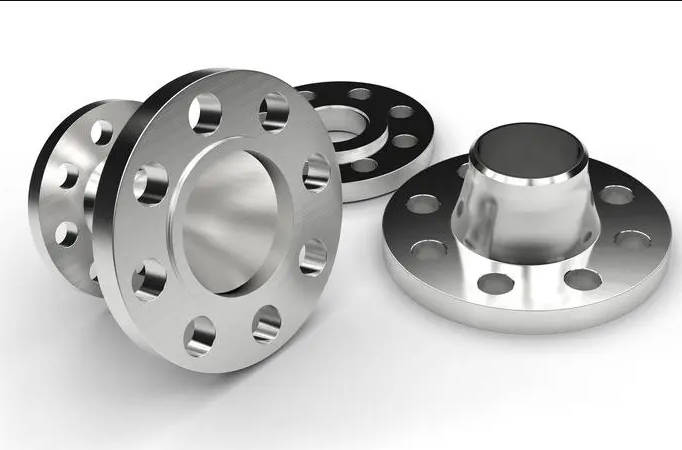
Understanding Quality Control in Metal Stamping
Quality control in metal stamping refers to the systematic processes and procedures that ensure the final products meet predefined quality standards. The significance of QC cannot be overstated, as it helps manufacturers deliver consistent, high-quality parts that fulfill customer requirements. By implementing effective quality control measures, companies can reduce defects, enhance operational efficiency, and build a strong reputation in the market.
Key Quality Control Measures in Metal Stamping
Material Inspection
The foundation of quality control begins with the selection of high-quality raw materials. Before production starts, it is essential to inspect materials thoroughly. This can involve visual inspections as well as various testing methods to verify material properties such as thickness, tensile strength, and composition. Ensuring that only quality materials enter the metal stamping processes is critical for producing reliable stamped components.
Process Monitoring
Monitoring the stamping process itself is another key aspect of quality control. This involves tracking various parameters during production to ensure they remain within specified limits. Techniques such as using sensors and automated systems can help monitor factors like pressure, temperature, and speed in real-time. By identifying deviations early, manufacturers can take corrective actions before defects occur.
Tooling and Die Maintenance
Tooling is a critical component of metal stamping that directly affects product quality. Regular maintenance and inspection of tools and dies are essential to prevent wear and tear that can lead to defects. Establishing a routine maintenance schedule ensures that tools are kept in optimal condition, which contributes significantly to the overall quality of the stamped products.
Implementing Statistical Process Control (SPC)
Statistical Process Control (SPC) is a powerful tool for enhancing quality control in metal stamping operations. SPC involves collecting data from the production process and analyzing it to identify variability. By using control charts to monitor performance over time, manufacturers can detect trends and make informed decisions regarding process adjustments. Implementing SPC not only improves product quality but also increases operational efficiency.
Training and Skill Development
To maintain high standards of quality control, it is crucial to invest in training and skill development for employees involved in the metal stamping processes. Regular training sessions on QC practices ensure that staff are aware of best practices and new technologies that can enhance product quality. A knowledgeable workforce is better equipped to identify potential issues and implement effective solutions. Please let me know when you would like me to continue!
Establishing a Quality Management System (QMS)
A robust Quality Management System (QMS) is essential for implementing effective quality control in metal stamping operations. A QMS encompasses a set of policies, processes, and procedures that organizations use to ensure their products meet quality standards. Adopting recognized standards, such as ISO 9001, can provide a structured approach to quality management.
Steps to Develop and Implement a QMS
- Define Quality Objectives: Establish clear quality objectives that align with customer expectations and regulatory requirements.
- Document Processes: Create detailed documentation of all processes involved in metal stamping, including inspection and testing protocols.
- Train Employees: Ensure that all employees understand the QMS and their roles within it through comprehensive training programs.
- Monitor Performance: Regularly review performance metrics to assess the effectiveness of the QMS and identify areas for improvement.
- Continuous Improvement: Foster a culture of continuous improvement by encouraging feedback and implementing changes based on data-driven insights.
By having a structured QMS in place, manufacturers can enhance their ability to produce high-quality stamped products consistently.
Customer Involvement in Quality Assurance
Engaging customers in the quality assurance process can lead to better outcomes for both manufacturers and buyers. Open communication regarding quality expectations is crucial. Manufacturers should actively seek customer feedback on product quality and incorporate this information into their QC practices.
Methods for Gathering Customer Feedback
- Surveys: Conduct surveys to gather insights on customer satisfaction regarding product quality.
- Regular Meetings: Schedule regular meetings with key customers to discuss quality issues and improvements.
- Performance Reviews: Share performance metrics with customers to demonstrate commitment to quality and transparency.
By involving customers in the quality assurance process, manufacturers can build stronger relationships and enhance their reputation for delivering high-quality metal stamping solutions.
Challenges in Quality Control for Metal Stamping
While implementing quality control measures is essential, manufacturers may face several challenges along the way. Common issues include:
- Resource Constraints: Limited budgets or personnel can hinder the implementation of comprehensive QC measures.
- Technology Integration: Difficulty in integrating new technologies into existing processes can pose challenges.
- Resistance to Change: Employees may resist adopting new QC practices or technologies.
Strategies to Overcome Challenges
- Invest in Training: Provide ongoing training to help employees adapt to new technologies and processes.
- Start Small: Begin with pilot projects to test new QC measures before full-scale implementation.
- Foster a Quality Culture: Encourage a culture that values quality at all levels of the organization, making it a shared responsibility.
By proactively addressing these challenges, manufacturers can improve their quality control processes and ensure higher standards of product excellence.
Conclusion
In conclusion, implementing effective quality control measures in metal stamping processes is essential for manufacturers aiming to deliver high-quality products that meet customer expectations. By focusing on material inspection, process monitoring, tooling maintenance, statistical process control, employee training, and establishing a robust QMS, companies can significantly enhance their QC efforts.
Furthermore, involving customers in the quality assurance process and addressing common challenges will contribute to building a reputation for reliability and excellence in the metal stamping industry. As potential buyers consider their options for purchasing metal stamping services, prioritizing suppliers who demonstrate strong quality control practices will ultimately lead to better outcomes. This article provides a comprehensive overview of how quality control can be effectively implemented in metal stamping processes. By following these guidelines, both manufacturers and buyers can benefit from improved product quality and operational efficiency.