Introduction
Quality control is a critical aspect of any manufacturing process, and metal stamping is no exception. As companies seek reliable Metal Stamping service providers to produce high-quality stamping parts, ensuring effective quality control measures is essential. This article aims to guide companies on how they can ensure quality control in their metal stamping operations, from material inspection to continuous improvement strategies.
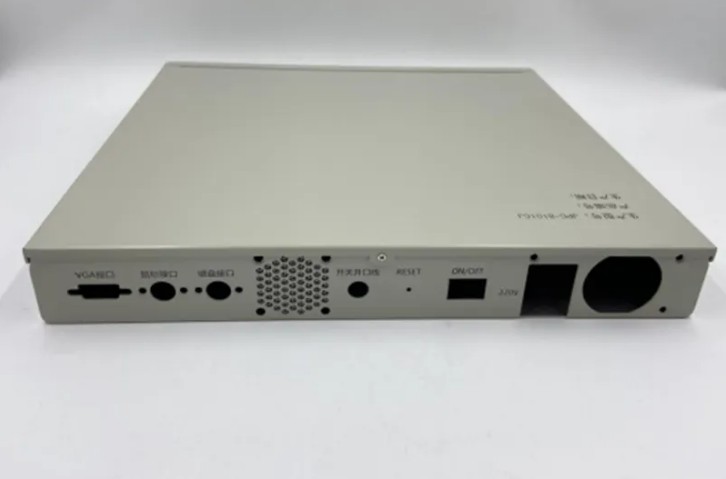
Understanding Metal Stamping
Definition and Process Overview
Metal stamping is a manufacturing process that involves the use of stamping dies and presses to cut, form, and shape metal sheets into desired shapes and sizes. The process involves several steps, including die design, material selection, and production techniques. Metal stamping is widely used in various industries, such as automotive, aerospace, and consumer electronics, to produce a wide range of stamping parts.
Importance of Quality in Metal Stamping
Quality control is crucial in metal stamping operations because it ensures the integrity and reliability of the final product. Defective stamping parts can lead to costly recalls, damaged reputations, and even safety hazards. By implementing effective quality control measures, companies can minimize the risk of defects, improve customer satisfaction, and maintain a competitive edge in the market.
Key Quality Control Measures in Metal Stamping
Material Inspection
One of the first steps in ensuring quality control in metal stamping is material inspection. Before the Stamping Process begins, it is essential to inspect the raw materials to ensure they meet the required specifications. This can include chemical composition analysis, mechanical testing, and visual inspection. By verifying the quality of the raw materials, companies can minimize the risk of defects and ensure consistent performance of the final product.
Process Monitoring
Monitoring the metal stamping process is another critical aspect of quality control. Companies can use sensors and automation to track key parameters such as pressure, temperature, and speed throughout the production process. This data can be used to identify potential issues and make adjustments to the process as needed. Regular maintenance and inspection of tooling and dies are also essential to ensure consistent quality and prolonged die life.
Tooling and Die Maintenance
Proper maintenance and inspection of tooling and dies are crucial for ensuring consistent quality in metal stamping operations. Dies can wear down over time due to repeated use, which can lead to defects in the final product. Regular maintenance, such as cleaning, lubrication, and replacement of worn parts, can help prolong die life and maintain consistent quality. Companies should also have a plan in place for die maintenance and replacement to minimize downtime and ensure continuous production.
Implementing Quality Control Systems
Establishing Quality Standards
Establishing clear quality standards is essential for ensuring consistent quality in metal stamping operations. These standards should be based on industry regulations, customer requirements, and best practices. By defining these standards upfront, companies can ensure that everyone involved in the production process is working towards the same goals and expectations.
Quality Management Systems (QMS)
Implementing a structured approach to quality management, such as a Quality Management System (QMS), can help companies streamline their quality control processes and ensure consistent results. QMS frameworks, such as ISO 9001, provide a comprehensive set of guidelines and best practices for managing quality throughout the organization. By adopting a QMS, companies can improve communication, reduce waste, and enhance overall efficiency.
Training and Employee Involvement
Employee training and involvement are critical components of effective quality control in metal stamping operations. Companies should provide regular training to their employees on quality standards, best practices, and problem-solving techniques. By empowering employees to take ownership of quality, companies can create a culture of continuous improvement and ensure that quality is a top priority throughout the organization.
Testing and Inspection Methods
In-Process Inspection
In-process inspection is a key component of quality control in metal stamping operations. Companies should have a plan in place for inspecting parts at various stages of the production process, such as visual inspection, dimensional checks, and functional testing. By catching defects early in the process, companies can minimize waste, reduce costs, and ensure that only high-quality parts are delivered to customers.
Final Product Testing
Final product testing is another essential aspect of quality control in metal stamping operations. Companies should have a plan in place for testing finished products to ensure they meet all required specifications and performance standards. This can include functional testing, stress testing, and other specialized testing methods depending on the application and industry requirements.
Statistical Process Control (SPC)
Statistical Process Control (SPC) is a powerful tool for analyzing production data and identifying trends and variations in the metal stamping process. By collecting and analyzing data on key process parameters, companies can identify potential issues early and make adjustments to the process as needed. SPC can also help companies identify opportunities for process improvement and optimize their operations for greater efficiency and quality.
Continuous Improvement Strategies
Feedback Loops
Establishing effective feedback loops is essential for continuous improvement in metal stamping operations. Companies should have a plan in place for collecting feedback from customers, end-users, and other stakeholders to identify areas for improvement and ensure that their products meet evolving needs and expectations. By closing the loop between production and customer feedback, companies can make data-driven decisions and continuously improve their metal stamping operations.
Root Cause Analysis (RCA)
Root Cause Analysis (RCA) is a powerful tool for identifying the underlying causes of defects or failures in the metal stamping process. By digging deeper into the root causes of quality issues, companies can implement targeted solutions that address the problem at its source. RCA can involve a variety of techniques, such as fishbone diagrams, 5 Whys analysis, and Pareto charts, to help companies identify and address the root causes of quality issues.
Lean Manufacturing Principles
Lean manufacturing principles can also be applied to enhance quality control in metal stamping operations. By eliminating waste, streamlining processes, and focusing on continuous improvement, companies can improve efficiency, reduce costs, and enhance overall quality. Lean principles can be applied to various aspects of the metal stamping process, such as material handling, tooling and die management, and employee training and development.
Choosing the Right Metal Stamping Partner
Evaluating Potential Suppliers
When choosing a metal stamping service provider, it is essential to evaluate their quality control practices and capabilities. Companies should look for metal stamping companies with a proven track record of delivering high-quality parts and a commitment to continuous improvement. They should also evaluate the supplier’s quality control processes, including material inspection, process monitoring, and testing and inspection methods.
Requesting Certifications and Documentation
Companies should also request certifications and documentation from potential metal stamping service providers to verify their quality control practices. This can include ISO certifications, quality control manuals, and process control plans. By reviewing this documentation, companies can gain a better understanding of the supplier’s quality control practices and ensure that they meet all required standards and regulations.
Conclusion
Ensuring quality control in metal stamping operations is essential for delivering high-quality products, meeting customer expectations, and maintaining a competitive edge in the market. By implementing effective quality control measures, such as material inspection, process monitoring, and continuous improvement strategies, companies can minimize the risk of defects, reduce costs, and enhance overall efficiency. When choosing a metal stamping service provider, it is essential to evaluate their quality control practices and capabilities to ensure that they can deliver the high-quality parts that meet all required specifications and performance standards.