Quality Control
in Metal Stamping
Explore KAIYAN comprehensive approach to ensuring top-notch quality control in every phase of the metal stamping process.
Quality Control in Metal Stamping
Ensuring Excellence at KAIYAN
Quality control (QC) in metal stamping is not just a step in the manufacturing process; it’s the backbone of production, ensuring the final products meet stringent standards and customer expectations. At KAIYAN, we understand the critical importance of quality control in maintaining our reputation as industry leaders. This article explores the various facets of quality control in metal stamping, illustrating how KAIYAN ensures excellence in every piece we produce.
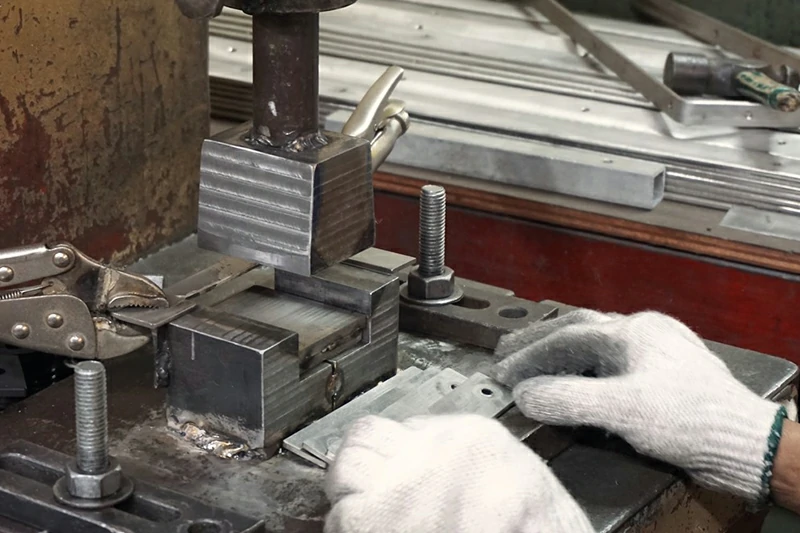
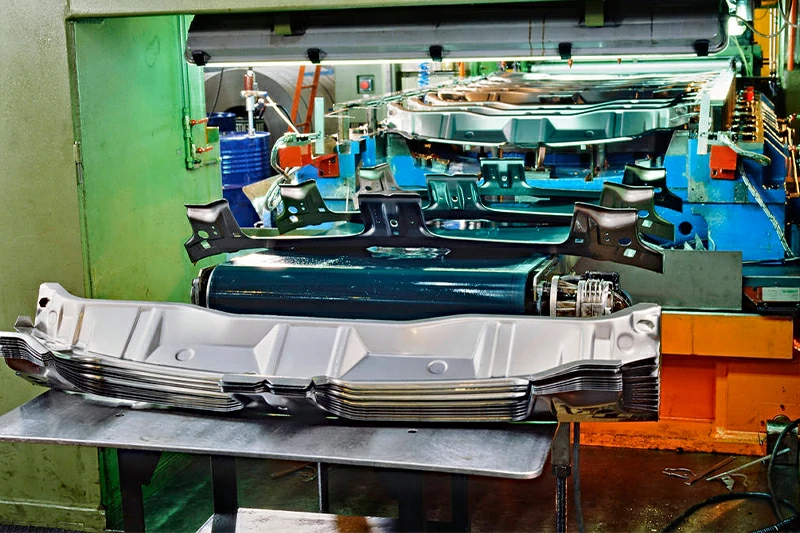
Quality Control
in Metal Stamping
Metal stamping involves converting flat metal sheets into specific shapes using a press and die set. This process can produce parts for various applications, from automotive components to consumer electronics. However, the precision and functionality of these parts hinge on rigorous quality control measures.
Quality control in metal stamping encompasses several key activities: material inspection, process monitoring, dimensional accuracy, surface finish evaluation, and part functionality tests. Implementing comprehensive QC procedures ensures that each stamped part is consistent, durable, and meets all specifications.
KAIYAN’s Approach to Quality Control
At KAIYAN, our quality control process begins even before the actual stamping takes place. Here’s how we ensure top-notch quality throughout our metal stamping operations

Material Inspection and Verification
Every project starts with the right materials. Upon receipt, we inspect all materials for defects, proper alloy, and thickness, ensuring they meet the predefined standards and specifications. This initial step prevents potential issues in later stages of production.

Design and Tooling Accuracy
We employ advanced CAD and CAM systems to design and manufacture our stamping dies. Before production runs, we conduct thorough inspections and trials to ensure the dies produce parts within tolerance limits and with the required features.

In-Process Monitoring and Control
Our stamping operations are closely monitored using state-of-the-art sensors and control systems. Parameters such as press force, speed, and material feed are continuously checked to maintain process stability and prevent deviations.

Dimensional Accuracy and Consistency
Each part is measured and inspected for dimensional accuracy using precision measuring instruments and gauges. Statistical process control (SPC) methods are employed to track and maintain consistency across batches, identifying trends and making necessary adjustments before deviations become problematic.

Surface Finish and Part Inspection
Beyond dimensions, the surface finish and overall appearance of each stamped part are scrutinized for imperfections like scratches, dents, or inconsistencies. This ensures that all products not only function as intended but also meet aesthetic standards.

Functionality and End-Use Testing
Depending on the application, parts may undergo additional testing to verify their functionality. This could include load-bearing tests, durability assessments, or specific operational trials to ensure they perform correctly in their intended environment.

Employee Training and Involvement
At KAIYAN, we believe that quality control is everyone’s responsibility. Our employees receive continuous training on QC best practices and are encouraged to take an active role in maintaining our high standards.

Feedback and Continuous Improvement
We maintain open lines of communication with our clients to receive feedback on the performance of our stamped parts. This feedback is integral to our continuous improvement processes, allowing us to make data-driven decisions and enhance our QC measures.
Challenges in Quality Control
Despite the clear benefits, maintaining stringent quality control in metal stamping presents challenges. Material variability, equipment wear, and human error can all impact quality. KAIYAN addresses these challenges by adopting a proactive approach, investing in technology, and fostering a culture of continuous improvement and accountability.
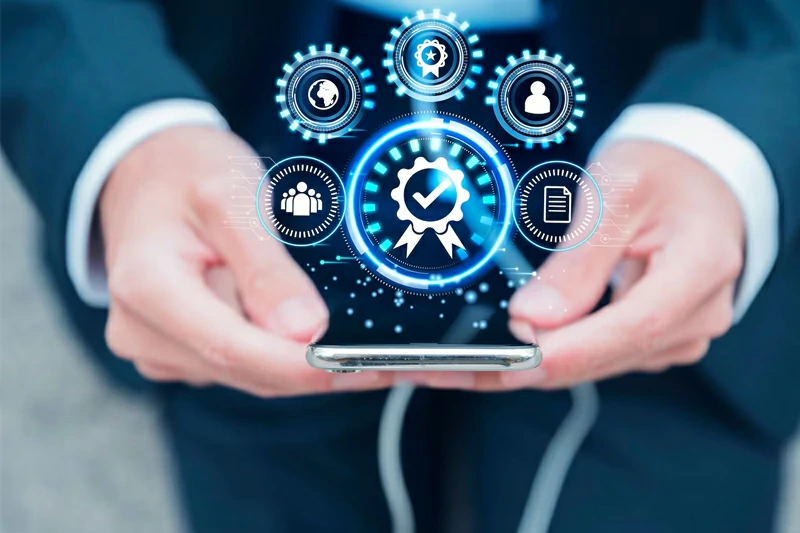
The Benefits of Rigorous Quality Control
Investing in comprehensive quality control measures has several benefits:
- Customer Satisfaction: Delivering high-quality parts leads to higher customer satisfaction and loyalty, key drivers for KAIYAN’s long-term success.
- Reduced Costs: By catching defects early, we minimize waste and avoid the costs associated with rework, returns, and warranty claims.
- Reputation and Competitiveness: Our commitment to quality sets KAIYAN apart from competitors, reinforcing our reputation as a trusted partner in the metal stamping industry.
- Operational Efficiency: Quality control helps streamline our operations, reducing downtime and increasing productivity.
- Compliance and Safety: Adhering to industry standards and regulations is non-negotiable. Our QC processes ensure that all products meet legal and safety requirements.
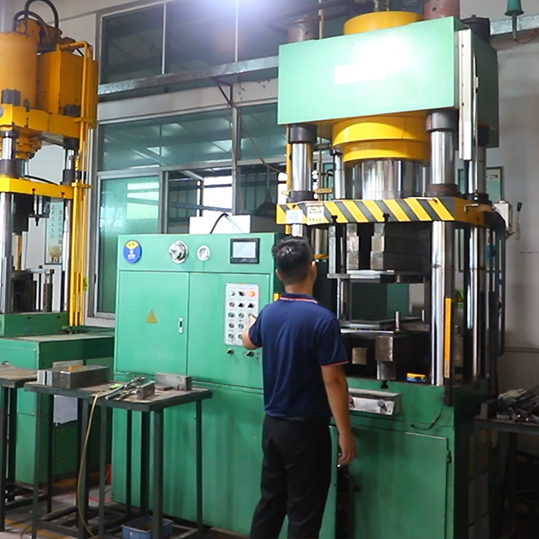