Introduction
The Stamping Process is a fundamental technique in precision engineering, widely used across industries to shape materials into desired forms with high accuracy. From automotive components to electronic parts, the quality and cost-effectiveness of products largely depend on the material used in the stamping process. Selecting the right material not only enhances the performance of the finished part but also ensures the efficiency of the Stamping Process service. This article explores the best materials for stamping in precision engineering, providing insights that will help buyers in choosing the right material for their specific needs.
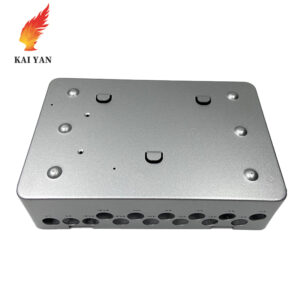
Importance of Material Selection in the Stamping Process
The choice of material plays a critical role in determining the success of the Stamping Process. Each material behaves differently under pressure and stress, and understanding these behaviors is key to ensuring high precision and durability. When the wrong material is selected, it can lead to undesirable results such as poor dimensional accuracy, increased wear on tooling, and higher costs in production.
In precision engineering, the material’s ability to hold tight tolerances, its reaction to mechanical stress, and its ability to undergo complex forming processes like deep drawing are crucial factors. The right material ensures not only the structural integrity of the final product but also the longevity of the Stamping Process factory equipment.
Common Materials Used in the Stamping Process
When considering materials for the Stamping Process, it’s essential to understand which ones are most commonly used in precision engineering. The selection depends on factors such as the part’s application, cost, and desired properties. Below are some of the most popular materials used by Stamping Process factories.
Metals
- Stainless Steel
Stainless steel is widely used in the Stamping Process service due to its excellent corrosion resistance, high strength, and versatility. It is commonly used in applications such as automotive components, kitchen appliances, and medical devices. Stainless steel also maintains its integrity under extreme conditions, making it ideal for precision parts where durability is essential. - Aluminum
Known for its lightweight properties, aluminum is highly malleable and easy to stamp. It is often chosen for parts that require flexibility, such as electrical enclosures and automotive parts. Aluminum’s lower cost compared to other metals also makes it a preferred material in high-volume Stamping Process projects, particularly when weight reduction is a critical factor. - Copper
Copper’s exceptional electrical conductivity makes it the material of choice for electrical connectors and electronic components. It is highly formable and can be stamped into intricate shapes with precision. Its ability to conduct heat also makes it ideal for components used in heat-sensitive environments. - Brass
Brass is a material that combines malleability with corrosion resistance. It is often used in applications where both function and aesthetics are important, such as decorative components, musical instruments, and plumbing parts. Brass can be easily stamped into complex shapes while maintaining a polished appearance, making it a popular choice in Stamping Process factories. - Carbon Steel
Carbon steel is one of the strongest and most durable materials used in stamping. It is ideal for heavy-duty applications where strength and toughness are required, such as in industrial machinery parts. Although it lacks the corrosion resistance of stainless steel, it is often chosen when strength and cost-effectiveness are prioritized.
Non-Metal Materials
- Plastics
While metals dominate the Stamping Process, certain plastics are also used in precision applications. Materials such as polycarbonate and ABS (Acrylonitrile Butadiene Styrene) can be stamped into specific shapes for use in electronics housings or consumer goods. Plastics are chosen for their lightweight properties and cost-effectiveness in large-scale production runs.
Key Factors to Consider When Choosing Stamping Materials
Selecting the best material for the Stamping Process depends on several factors. Understanding these considerations can help ensure the final product meets the required specifications while staying within budget.
Material Thickness
The thickness of the material impacts how it can be shaped during stamping. Thinner materials are easier to form and require less force, making them suitable for intricate designs. On the other hand, thicker materials require stronger presses and more robust tooling, often leading to higher costs. Precision stamping services often offer guidance on the optimal material thickness for specific applications.
Material Hardness and Ductility
Materials with high hardness, like carbon steel, offer strength but may be more difficult to stamp, requiring specialized tooling. In contrast, more ductile materials, like aluminum or copper, can be easily shaped without the risk of cracking or fracturing during the Stamping Process service. Matching the material’s hardness and ductility to the complexity of the part being produced is crucial for achieving high precision.
Material Cost
The cost of materials is another key factor. While high-performance metals like stainless steel or advanced alloys may offer superior strength and corrosion resistance, they can also be more expensive. Businesses should balance material costs with the desired quality and durability of the finished product. Opting for a less expensive material may result in reduced performance, but higher-cost materials can elevate the quality of the Stamping Process output.
End Use Requirements
Every material has specific properties that make it suitable for certain applications. For example, products that will be exposed to harsh environments, such as marine or industrial applications, may require materials with excellent corrosion resistance, like stainless steel. Conversely, for parts that need to be lightweight but strong, aluminum may be the preferred option. The final use of the product is a major determinant in the material choice.
Material-Specific Challenges in Precision Stamping
Springback
Springback refers to the tendency of a material to return to its original shape after being stamped. Materials like high-strength steel are particularly prone to this phenomenon, which can cause dimensional inaccuracies. To counteract springback, Stamping Process factories often adjust tooling or apply additional processes to ensure precision.
Tooling Wear
Some materials, especially harder ones like carbon steel, can cause significant wear on stamping tools, increasing maintenance costs and downtime. Choosing the right combination of material and tooling can help minimize wear and extend the lifespan of the equipment. Many Stamping Process services specialize in optimizing tooling setups for different materials to reduce the impact of wear.
Surface Finish
The material’s surface properties can affect the final appearance of stamped parts. Some metals, such as brass, naturally maintain a high-quality finish, while others may require post-stamping treatments like polishing or coating to achieve a desired aesthetic. Stamping Process factories often provide finishing services to improve the appearance and durability of the stamped parts.
Innovations in Materials for Stamping
Advances in material science have introduced new high-performance materials to the Stamping Process. Metals like titanium and magnesium alloys are gaining popularity for their strength-to-weight ratios, offering enhanced performance for industries like aerospace and automotive. These innovative materials provide new possibilities for precision engineering, allowing for lighter, stronger, and more corrosion-resistant parts.
Conclusion
Choosing the right material for the Stamping Process is critical to the success of precision engineering projects. Factors such as material thickness, hardness, ductility, and cost all play a vital role in determining the performance and durability of stamped parts. Stamping Process services are well-versed in guiding clients through material selection, ensuring that the final product meets both technical and budgetary requirements. With continuous innovations in materials, businesses have more options than ever before to improve the quality and efficiency of their stamped components.