Introduction
In modern manufacturing, the Stamping Process plays a crucial role in shaping metals into usable components for various industries. Whether you’re in the automotive, electronics, or aerospace sector, choosing the right Stamping Process service can significantly impact the quality, cost, and efficiency of your products. Among the most widely used techniques are cold and hot stamping, each with distinct advantages and challenges. Understanding these differences is essential for businesses looking to work with a Stamping factory to meet their specific production needs.
This article will explore the key differences between cold and hot stamping, helping you make informed decisions when purchasing Stamping Process services for your manufacturing projects.
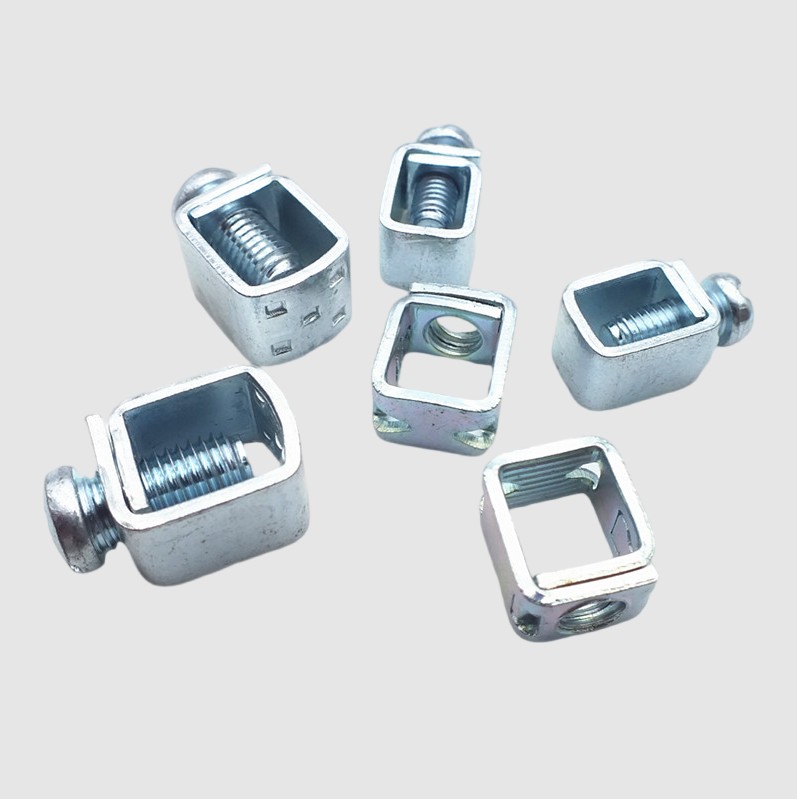
Overview of Cold Stamping Process
Definition and Process
Cold stamping is a widely used technique that involves shaping metal sheets at room temperature through pressing, bending, and cutting operations. This process is performed using a mechanical or hydraulic press, and it allows for the creation of parts with high precision. Cold stamping is particularly popular in high-volume production settings due to its speed and cost-effectiveness.
Materials Used
Typical materials used in cold stamping include metals like steel, aluminum, and copper. These materials are generally softer and thinner, making them suitable for forming without the need for heating. This is especially beneficial for industries that require large quantities of parts, such as consumer electronics or household appliances.
Advantages of Cold Stamping
One of the key advantages of cold stamping is its ability to produce parts quickly and cost-effectively. The absence of heating processes results in lower energy consumption and faster production cycles, making it an ideal choice for high-volume manufacturing. Cold stamping also provides excellent dimensional accuracy, making it suitable for products that require detailed shapes or tight tolerances.
Challenges in Cold Stamping
However, cold stamping does come with some limitations. The process is generally less effective when working with thicker metals or materials that are prone to cracking. Additionally, complex shapes can be difficult to achieve with cold stamping, especially if the metal’s elasticity is a concern. For these reasons, businesses seeking more intricate or durable parts may opt for other Stamping Process services.
Overview of Hot Stamping Process
Definition and Process
Hot stamping is a more specialized Stamping Process that involves heating metal to a high temperature before shaping it. This process is commonly used in industries that require high-strength materials, such as the automotive and aerospace sectors. During hot stamping, the metal is heated until it becomes malleable, then formed into the desired shape using a press. As the metal cools, it undergoes a heat treatment that significantly increases its strength and durability.
Materials Used
The materials typically used in hot stamping are high-strength steels and other alloys that require elevated temperatures to be effectively formed. These materials are not only harder to shape at room temperature but also benefit from the enhanced strength provided by the heat treatment during the hot stamping process.
Advantages of Hot Stamping
The most notable advantage of hot stamping is the increase in material strength after the process is completed. By heating the metal, hot stamping allows for the formation of more complex shapes and geometries that would be impossible to achieve with cold stamping. This is why the Stamping factory responsible for automotive parts often prefers hot stamping, as it produces components that are more durable and capable of withstanding extreme conditions.
Challenges in Hot Stamping
Hot stamping, however, comes with its own set of challenges. The need for heating means higher energy consumption and slower production times compared to cold stamping. Additionally, hot stamping requires more complex tooling and machinery, which can increase the cost of the Stamping Process service. For businesses working with tight budgets or high production volumes, these factors need to be carefully considered.
Key Differences Between Cold and Hot Stamping
Temperature Requirements
The primary difference between cold and hot stamping lies in the temperature at which the process is carried out. Cold stamping is performed at room temperature, whereas hot stamping requires heating the metal to high temperatures before forming. This distinction affects both the types of materials that can be used and the final properties of the product.
Material Suitability
Cold stamping is more suitable for softer, thinner metals like aluminum or copper, making it ideal for less complex parts. On the other hand, hot stamping is better for high-strength metals like steel that benefit from heat treatment, enabling the formation of more intricate shapes. When choosing a Stamping Process service, it’s important to consider the material you’ll be working with to determine which process is more appropriate.
Cost Considerations
In terms of cost, cold stamping generally requires lower operational expenses due to its faster production speed and absence of heating. Hot stamping, while offering stronger parts, comes with higher energy costs and more complex tooling requirements. Therefore, businesses should balance their need for strength and complexity with their budget when selecting a Stamping factory.
Production Speed and Efficiency
Cold stamping is typically faster and more efficient for high-volume production. However, it is limited by the thickness and type of material that can be used. Hot stamping, while slower, produces parts that are stronger and can handle more complex designs. Understanding these trade-offs is key when purchasing Stamping Process services.
Choosing Between Cold and Hot Stamping for Your Needs
Factors to Consider
When deciding between cold and hot stamping, several factors should be considered, including the material type, the complexity of the design, the required production volume, and budget constraints. For instance, if you are working with softer metals and need a high production rate, cold stamping may be the better option. On the other hand, if you need stronger, more intricate components, hot stamping might be the right choice.
Industry-Specific Recommendations
Different industries will find different benefits in cold and hot stamping. For example, electronics and consumer goods manufacturers often use cold stamping for its speed and cost efficiency. Meanwhile, the automotive and aerospace sectors favor hot stamping due to the need for high-strength, durable parts.
How to Select a Stamping Service Provider
Assess Expertise and Capabilities
When selecting a Stamping Process service, it’s essential to assess the provider’s expertise and capabilities. A reliable Stamping factory should have experience in your specific industry and the ability to handle both cold and hot stamping, depending on your needs. Additionally, ensure that the factory uses the latest technology to maintain precision and quality in every part they produce.
Evaluate Cost vs. Quality
Cost is always a factor, but it’s equally important to evaluate the quality of the parts produced. If your project demands high precision and strength, it may be worth investing in a Stamping Process service that specializes in hot stamping, even if it comes with higher costs. For simpler parts, cold stamping may offer the best balance between quality and cost-efficiency.
Customization and Support
Look for a Stamping factory that can offer customization services to fit your specific requirements. Whether it’s creating custom tooling or providing technical support throughout the production process, a provider that goes beyond standard stamping can add significant value to your project.
Conclusion
Both cold and hot stamping offer distinct advantages, and the choice between the two depends on your specific project requirements. Cold stamping is ideal for high-volume production of simple parts, while hot stamping excels in creating strong, complex components for industries like automotive and aerospace. When purchasing Stamping Process services, it’s essential to consider factors like material type, production volume, and budget to make the best decision.
By understanding the differences between cold and hot stamping, you’ll be better equipped to choose the right Stamping factory for your needs, ensuring you receive high-quality components that meet your specifications.